INTRODUCTION
The wheel is an important part of the crane, which runs on the track and bears the dead weight and load of the crane. Crane wheel material should have high strength, high hardness and good wear resistance.
Crane wheel is divided into single rim wheel, double rim wheel and missing wheel. Single flange wheel is mainly used in gantry crane under 5t, double beam gantry bridge crane trolley running mechanism; Double rim wheel is mainly used in gantry crane, double beam bridge gantry crane, crane operation mechanism, casting crane operation mechanism, electric flat car, platform car group, ship unload, shipyard, port machine, coal unload, stacking and taking machine, bridge machine and so on.
The materials used for the wheels are mainly forgings and ductile iron. The forging has a large carrying capacity and can be applied to lifting surfaces with severe working conditions such as metal cranes. The forged wheel set optimizes the structure and performance of the metal blank through forging and pressing machinery to eliminate the defects of the structure, so the overall performance of the forged wheel is better than the cast wheels of the same material. Nowadays, many crane manufacturers use nodular cast iron as the main material of the wheels, because the internal structure of the nodular cast iron itself is in the form of spheroidization and has high strength, and because of the high carbon content of the cast iron and good wear resistance, it is more suitable for lifting conditions In addition, graphite has a lubricating effect, so nodular cast iron wheels are favored by more and more users.
Our wheel heat treatment can be done in 3 ways according to different requirements. The first is the overall quenching and tempering treatment, wheel tread hardness of HB300-380, mainly used for standard crane products; The second is surface medium frequency quenching and tempering treatment, the wheel tread hardness is HB300-380, can also do HRC45-55, mainly used in the requirements of the wheel center hardness is low, the tread requirements are high, not suitable for the overall heat treatment products; The third is the overall quenching and tempering treatment. The hardness of the wheel tread can be up to HRC50-56. Due to the different raw materials selected, the hardness of the wheel tread will decay with the depth layer.
Production Process
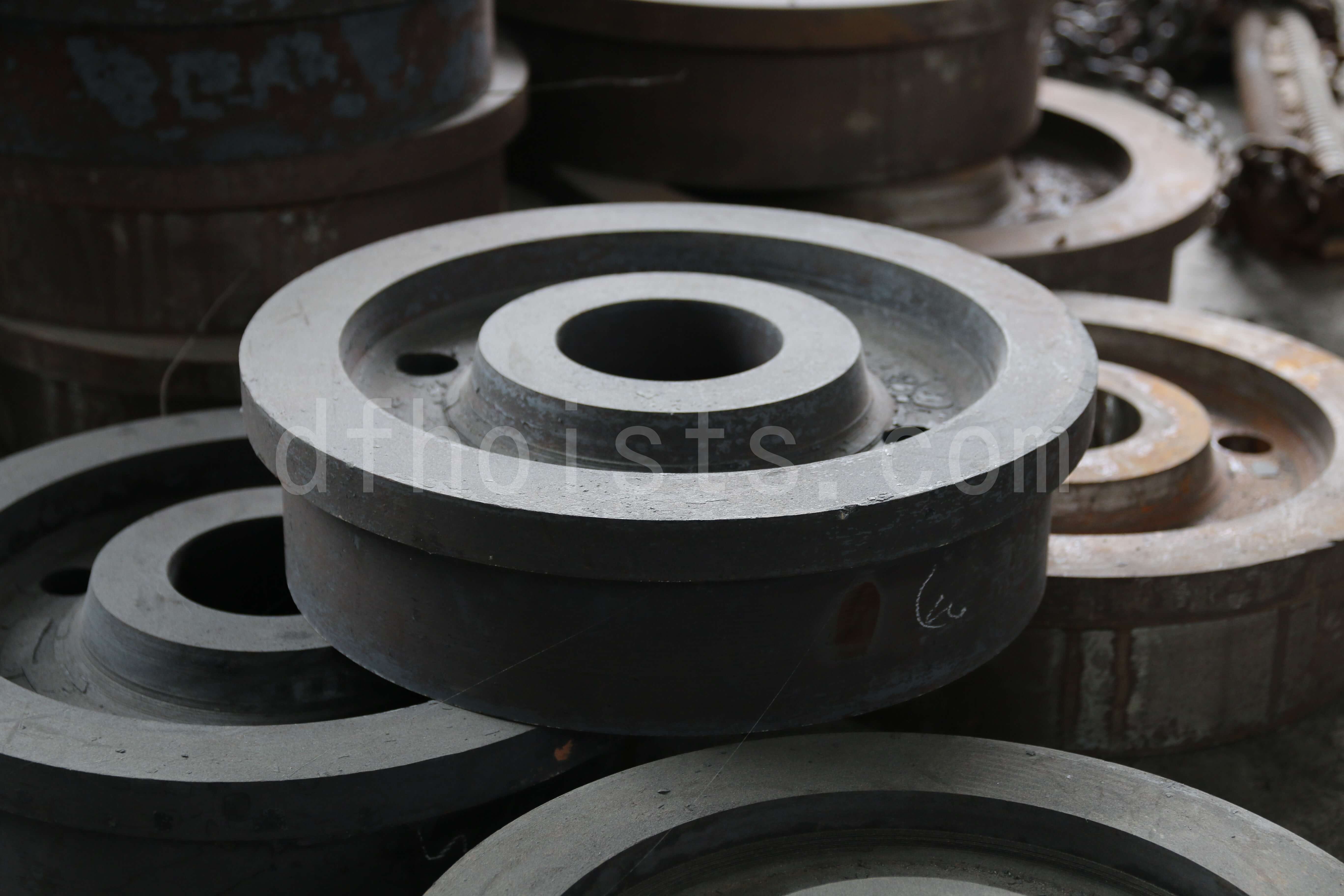
workblank
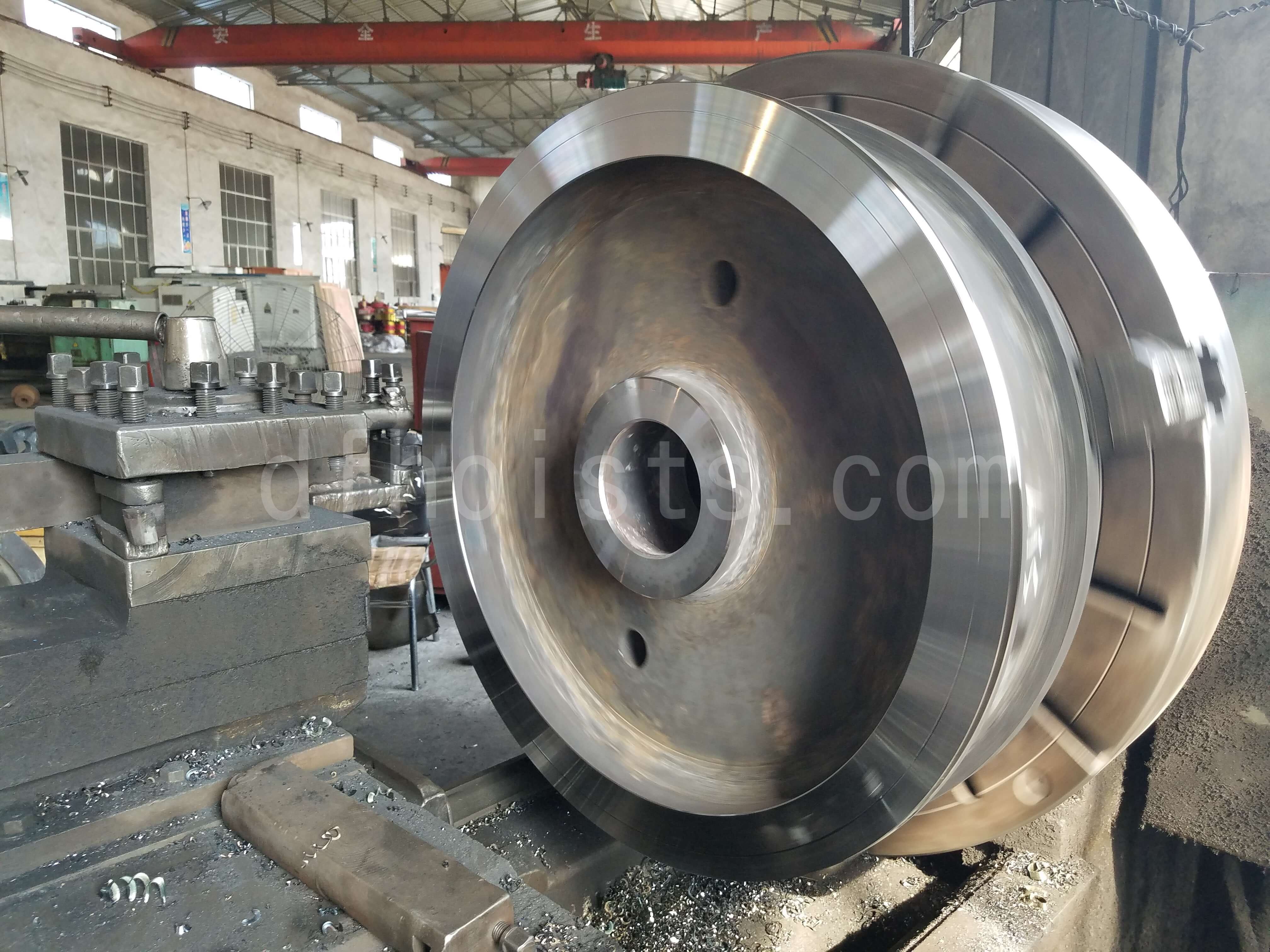
rough machining
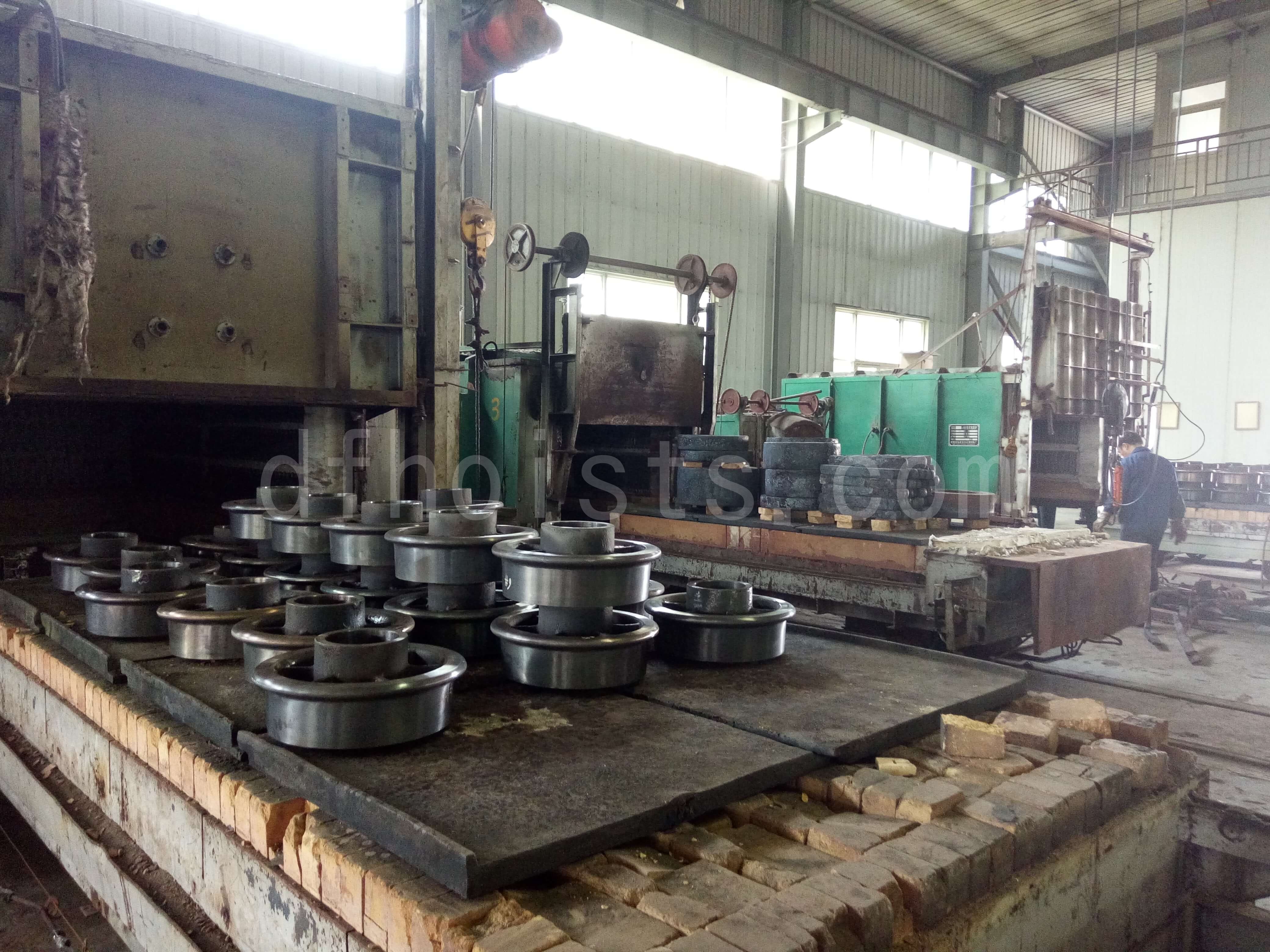
heat treatment
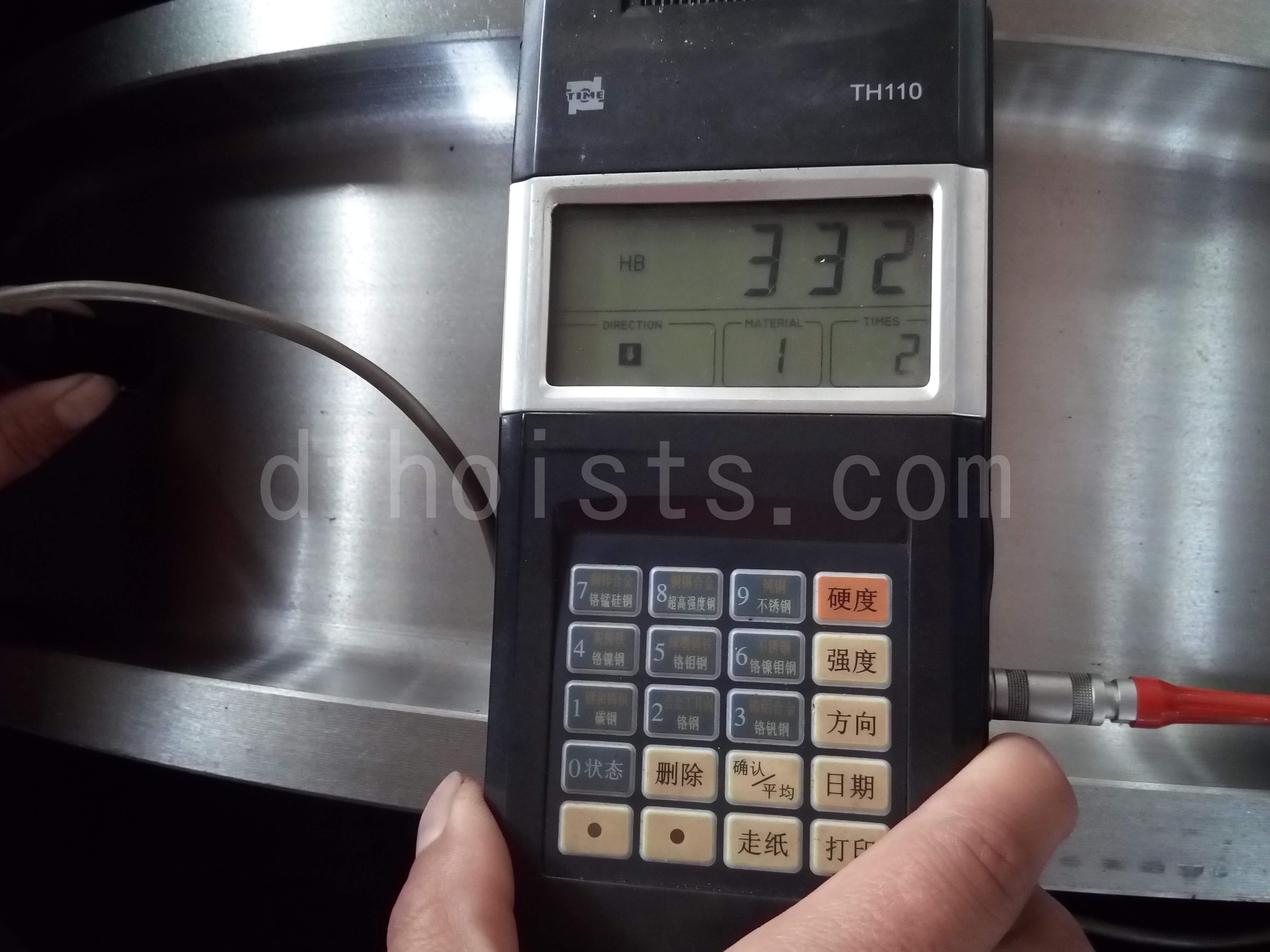
hardness test
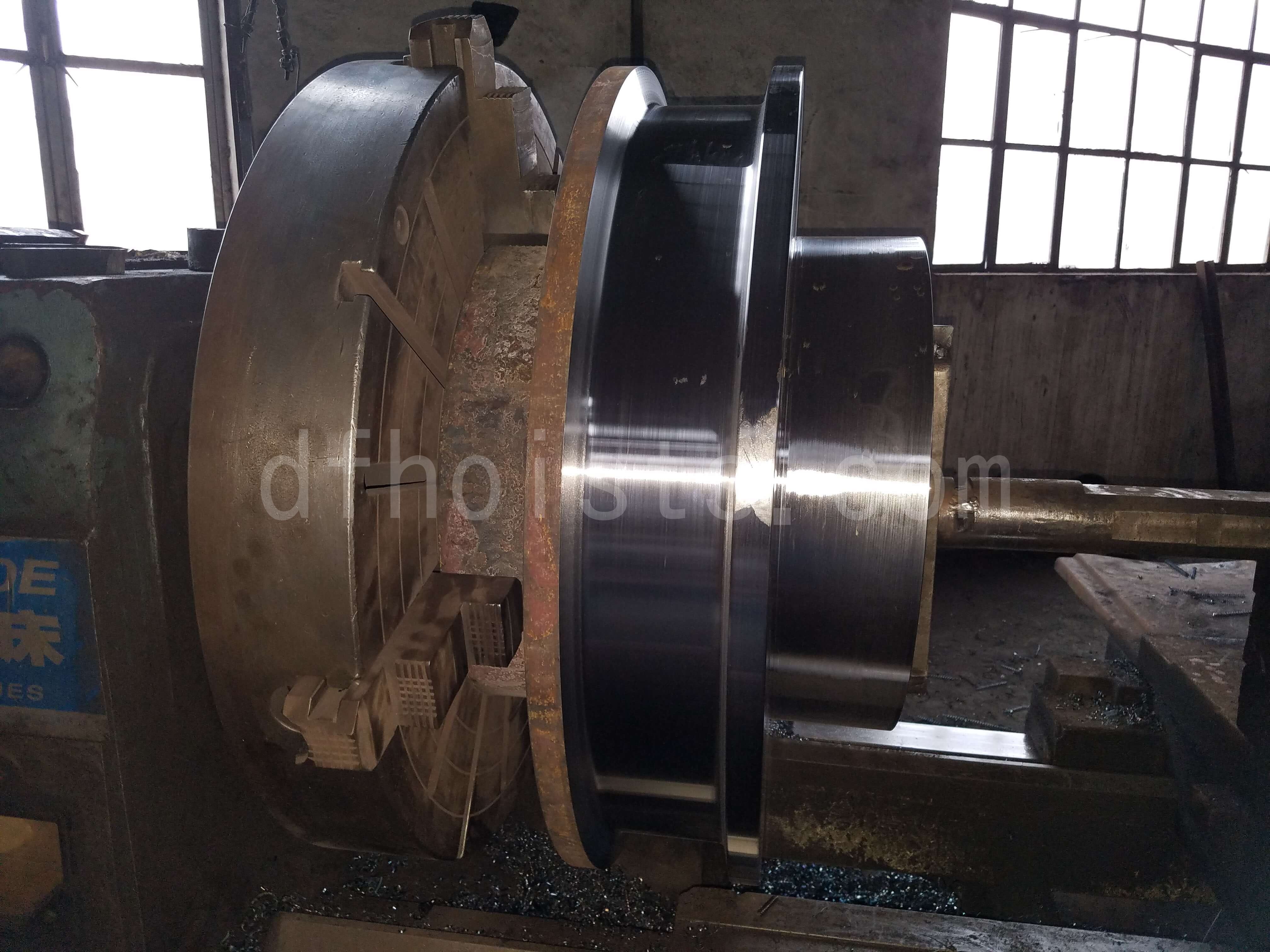
finish machining
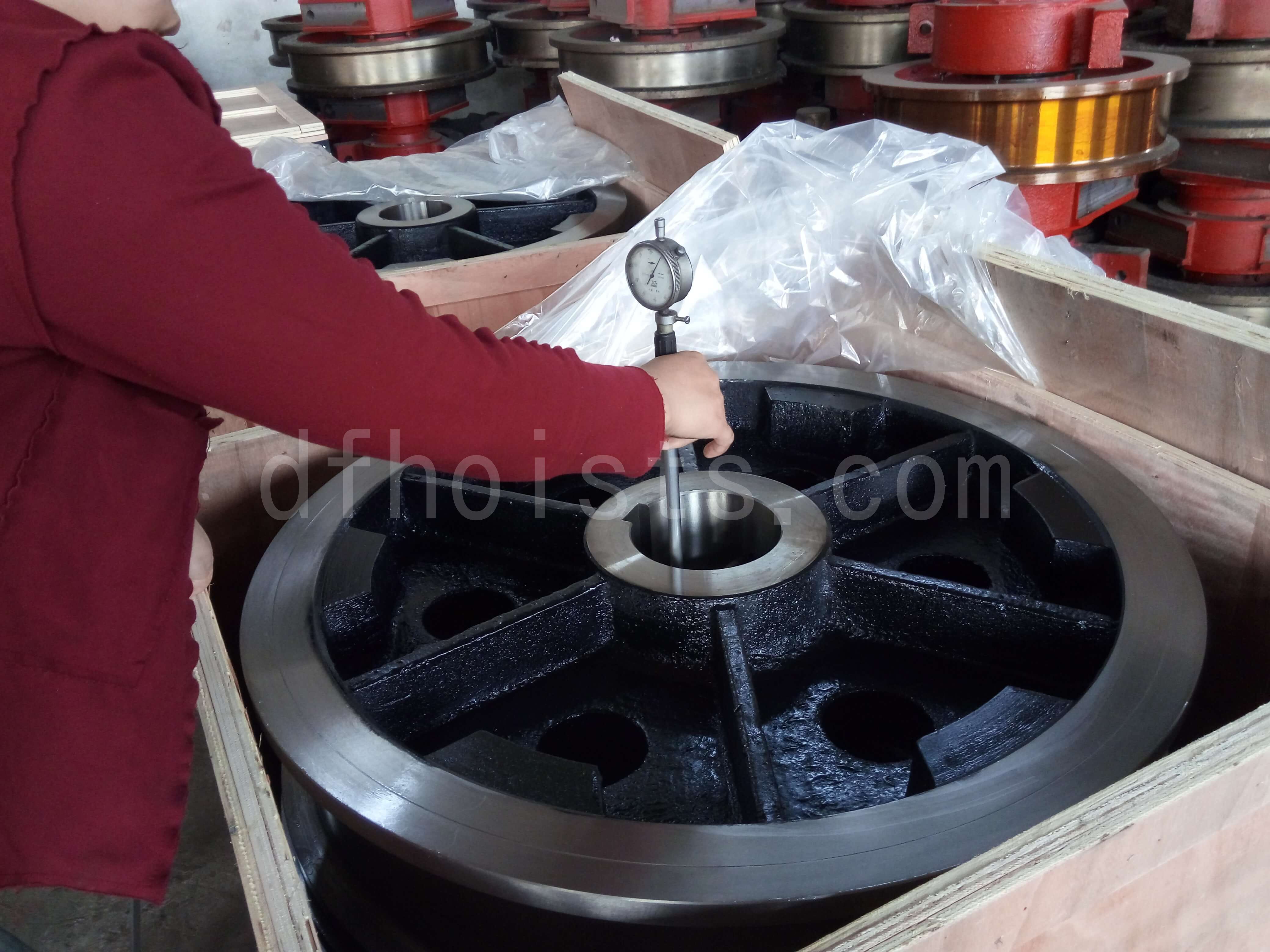
dimension test
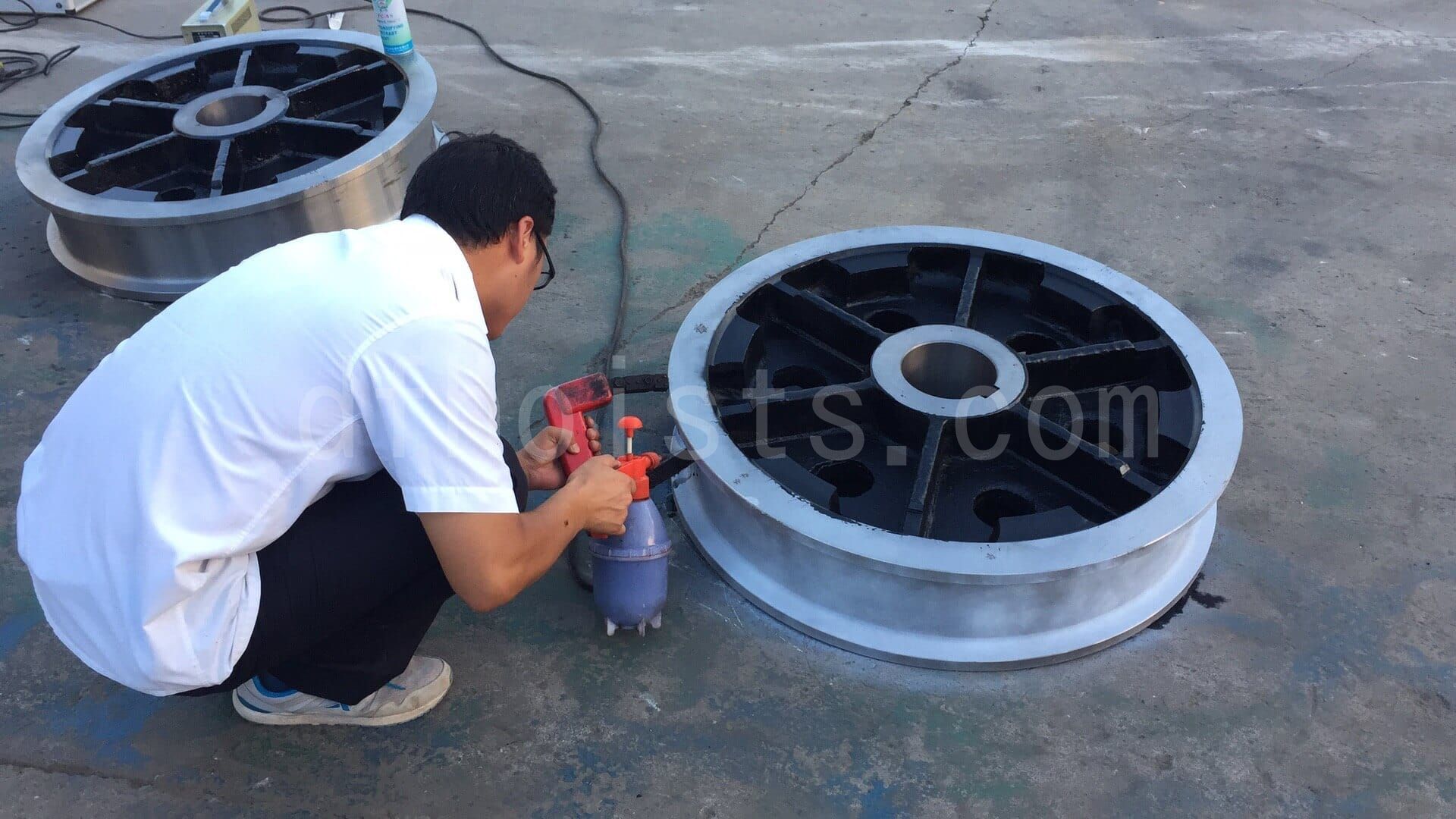
non-distructive test
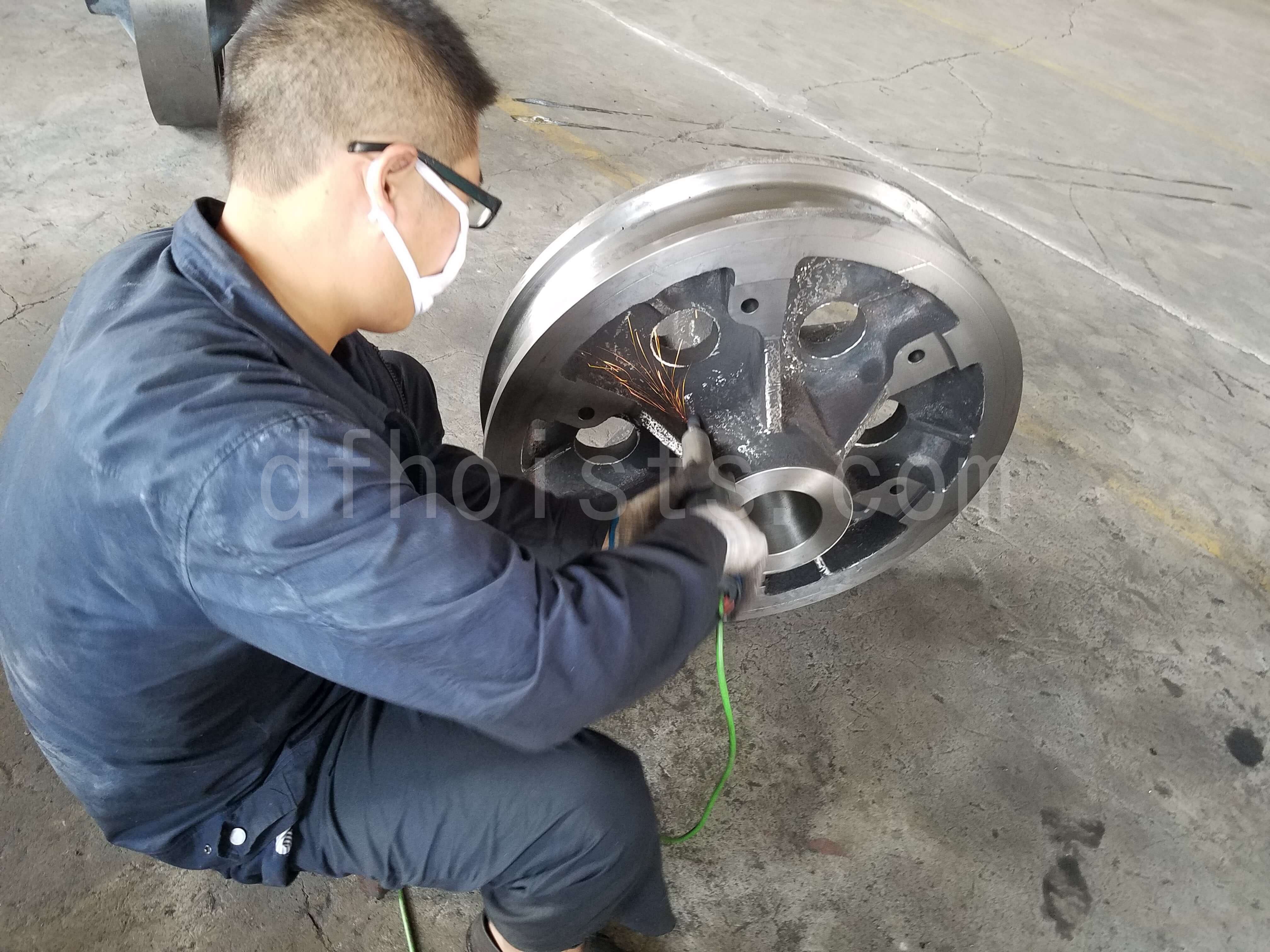
polishing
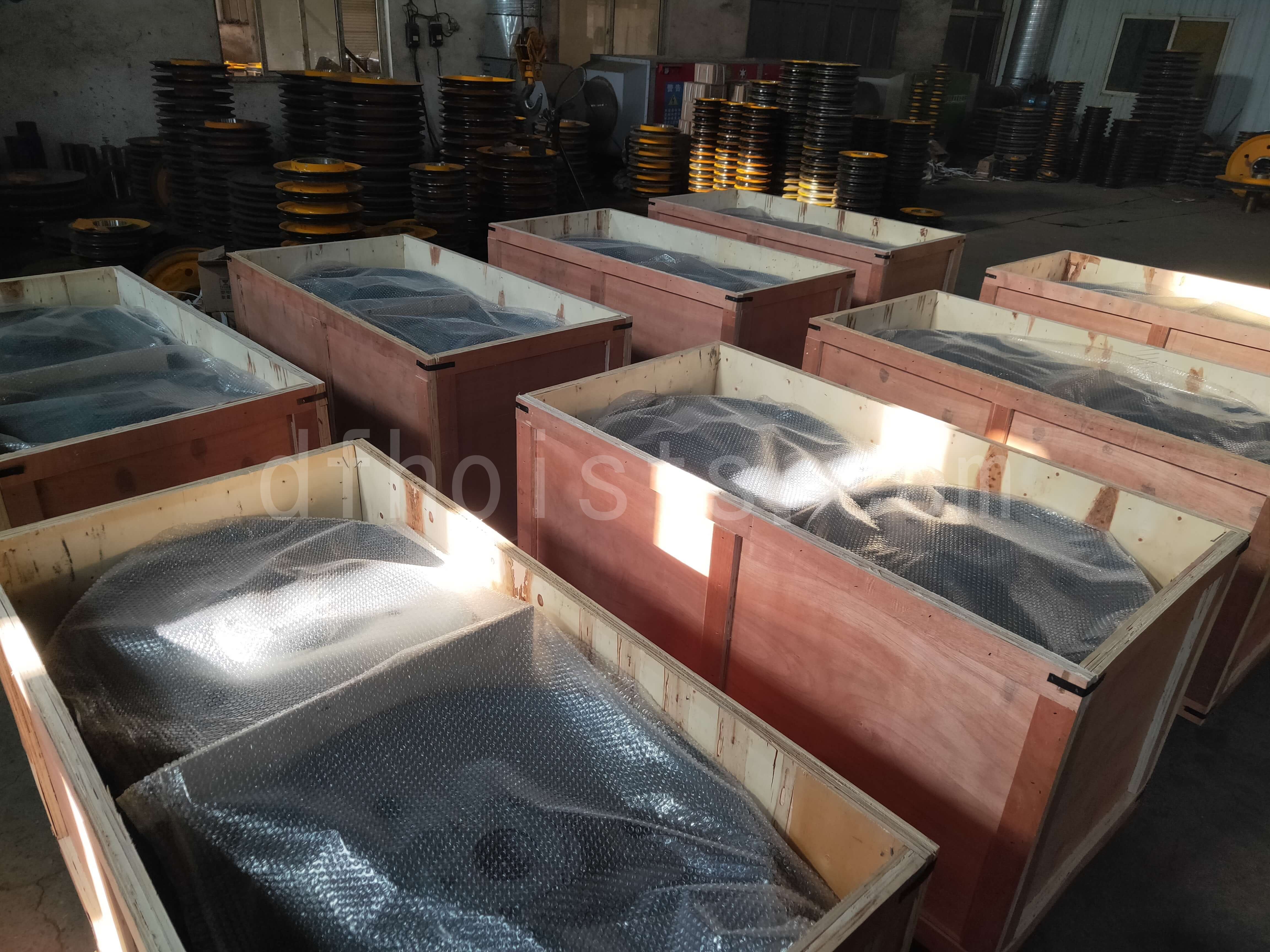
packing and delivering